Maintaining sterility cannot be overstated in the complex world of pharmaceutical manufacturing. It is a critical factor in ensuring the safety and efficacy of medicinal products. At every stage, from production to distribution, stringent standards are in place to prevent microbial contamination and preserve product integrity. One of the most crucial steps in this process is sealing IV bottle caps, where the choice of materials is of utmost importance. With its unique properties, aluminum foil is a key player in ensuring sterility in IV bottle caps. This comprehensive guide delves into how aluminum foil achieves this crucial objective, using advanced techniques like latent semantic indexing and natural language processing to provide valuable insights.
1. Barrier Properties:
1. Barrier Properties: Aluminum foil stands out with its exceptional barrier properties, effectively blocking the transmission of moisture, oxygen, light, and microorganisms. When used in IV bottle cap sealing, aluminum foil forms an impermeable barrier that prevents external contaminants from infiltrating the sterile contents within the bottle. This unique barrier function is essential for maintaining the sterility of pharmaceutical products, safeguarding them against microbial ingress throughout their shelf life.
2. Hermetic Sealing:
Hermetic sealing refers to a container’s complete and airtight closure, effectively isolating its contents from the external environment. Aluminum foil achieves hermetic seals when applied to IV bottle caps, ensuring no air or contaminants can penetrate the sealed enclosure. By creating an airtight barrier, aluminum foil plays a crucial role in preserving the sterility of pharmaceutical formulations, minimizing the risk of contamination during storage and transportation.
3. Compatibility with Sterilization Methods:
Sterilization is a fundamental process in pharmaceutical manufacturing to eliminate microbial contaminants from equipment, packaging materials, and product surfaces. Aluminum foil is compatible with various sterilization methods, including autoclaving, gamma irradiation, and ethylene oxide sterilization. Unlike certain plastics or elastomers, aluminum foil can withstand high temperatures and radiation exposure without compromising its barrier properties or structural integrity, ensuring that IV bottle caps remain sterile throughout sterilization.
5. Tamper Evidence:
Ensuring the integrity of pharmaceutical packaging is essential for detecting and deterring tampering attempts. Aluminum foil seals indicate tampering, as any attempt to breach the seal would result in noticeable damage or alteration. This tamper-evident feature enhances security and trust in pharmaceutical products, allowing healthcare professionals and consumers to verify the authenticity and sterility of the contents.
6. Regulatory Compliance:
In the highly regulated pharmaceutical industry, adherence to strict guidelines governing packaging materials and processes is non-negotiable. Aluminum foil seals are a testament to this, as they meet the regulatory requirements set forth by organizations such as the FDA and EMA. By choosing aluminum foil for IV bottle cap sealing, pharmaceutical manufacturers can demonstrate their commitment to regulatory compliance and patient safety, ensuring that IV bottle caps meet the necessary standards for sterility and product safety.
7. Extended Shelf Life:
Maintaining sterility plays a crucial role in prolonging the shelf life of pharmaceutical products. Aluminum foil seals effectively prevent microbial contamination, thereby preserving the sterility and stability of IV formulations. By extending the medication’s shelf life, aluminum foil reduces waste and enhances patient access to essential treatments.
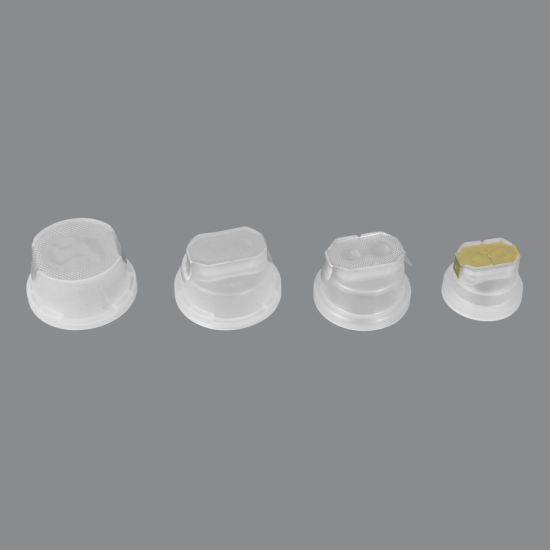
In conclusion
aluminum foil is a cornerstone in ensuring the sterility of IV bottle caps in pharmaceutical manufacturing. Through its superior barrier properties, hermetic sealing capabilities, and compatibility with sterilization methods, aluminum foil is vital in safeguarding pharmaceutical products against microbial contamination and maintaining product integrity. By embracing aluminum foil as a sealing solution, pharmaceutical manufacturers can uphold the highest standards of sterility, regulatory compliance, and patient safety throughout the product lifecycle.
Aluminum foil