Introduction:
In the realm of medical consumable manufacturing, the production of dialysis catheters holds significant importance. These vital devices serve as lifelines for individuals undergoing hemodialysis treatment, necessitating precision and quality throughout the manufacturing process. In this article, we’ll delve into the intricacies of dialysis catheter manufacturing, highlighting key points to consider for optimal production.
Understanding the Dialysis Catheter Manufacturing Process:
1. Material Selection:
– The choice of materials plays a critical role in the performance and biocompatibility of dialysis catheters. Medical-grade materials such as silicone or polyurethane are commonly used due to their flexibility, durability, and compatibility with the human body.
– Selecting materials with the appropriate mechanical properties, such as tensile strength and elasticity, is essential to ensure the catheter can withstand the rigors of insertion and removal without compromising integrity.
2. Design and Engineering:
– The design phase involves conceptualizing the catheter’s structure, dimensions, and features to meet specific medical requirements and regulatory standards.
– Engineering considerations include optimizing the catheter’s internal lumen for efficient blood flow, minimizing the risk of kinking or occlusion, and incorporating features to enhance patient comfort and safety.
– Utilizing advanced CAD (Computer-Aided Design) software allows for precise modeling and simulation, facilitating iterative improvements and validation before proceeding to manufacturing.
3. Manufacturing Techniques:
– Catheter manufacturing typically involves a combination of extrusion, molding, and assembly processes.
– Extrusion: Medical-grade polymers are extruded into hollow tubes, forming the main body of the catheter. Tight control over extrusion parameters is crucial to ensure uniformity and dimensional accuracy.
– Molding: Components such as catheter tips, connectors, and side ports are molded using injection molding or overmolding techniques. Attention to detail during molding is essential to achieve consistent quality and minimize defects.
– Assembly: The various components of the catheter, including lumens, side holes, and connectors, are meticulously assembled using automated machinery or skilled technicians. Quality control measures, such as visual inspection and testing, are implemented at each stage to detect any anomalies and ensure compliance with specifications.
4. Regulatory Compliance:
– Manufacturing dialysis catheters requires adherence to stringent regulatory guidelines, including those set forth by regulatory bodies such as the FDA (Food and Drug Administration) in the United States.
– Manufacturers must maintain documentation of the entire manufacturing process, including materials used, manufacturing procedures, quality control measures, and testing protocols.
– Rigorous testing, including biocompatibility testing, mechanical testing, and sterility assurance, is conducted to validate the safety, efficacy, and performance of the catheters before they are released for distribution.
Conclusion:
Manufacturing dialysis catheters demands meticulous attention to detail, from material selection and design to production and quality control. By adhering to best practices and regulatory standards, manufacturers can ensure the production of high-quality catheters that meet the needs of healthcare providers and patients alike. As a leading supplier of machines for medical consumable manufacturing, we recognize the importance of precision and excellence in the production of dialysis catheters, and we remain committed to supporting manufacturers in their quest to improve patient outcomes and enhance renal health.
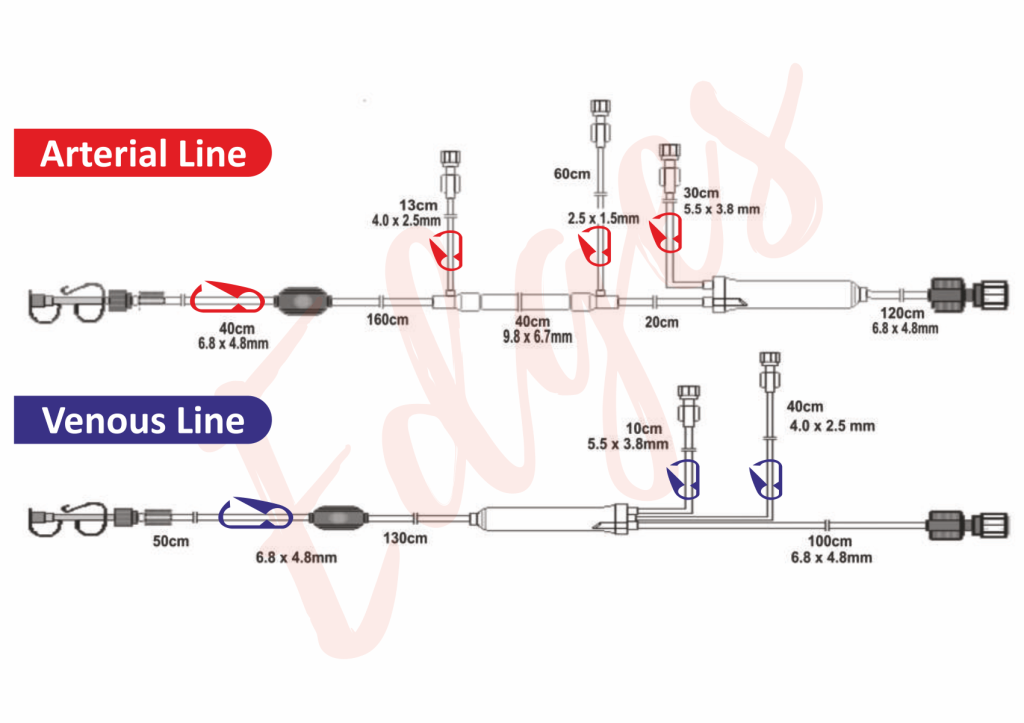
Tube/catheter assembly line